An Innovative Revolution of Impact Wrench Torque Control
Making the torque control easy and affordable
No more precision and costly torque-controlled tools required, regardless of air tool brand, manufacturer, design, and grade.
Applicable to
Any Air Driven Continuous & Discontinuous Torque Tools
Air Clutch Tools
Air Impact Driver
Air Impact Ratchet
Air Pulse Wrenches
Air Impact Wrenches
Geared Wrench / Torque Multipliers
&
Electrical / Cordless Tool with auto-shutoff Torque Control Mechanism
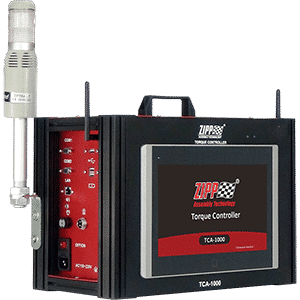
ZIPPTORK products Features
Torque Controller – TCA
With patented control algorithm and device for controlling the output torque of air impact wrenches, air impact ratchet wrenches, air pulse tools, as well as geared torque multipliers. Regardless of brand or manufacturer and even the type of impact mechanism. It is designed with stability, safety, and accuracy in mind.
Key Features
Easy set-up in minutes
Dynamic torque controllable accuracy:± 5% ~ ±15%
Patented control algorithm and device~ applicable to any air-driven impact or pulse tool regardless of brand and type of impact mechanism
Automatic air consumption rate measurement and selection for the broadest torque control range ( TCA only )
Optional programmable function for bolting sequence control while applying with the tagged bolt or sensing bolt
Built-in torque fastening stage & bolting sequence control
Built-in preset parameters and job sequences up to 10 tools for the ease of assembly works
Versatile operation modes for option: ◆Air impact wrench ◆Air pulse tool ◆Torque wrench ◆Clutch tool ◆Geared wrench/torque multiplier ◆Torque tester
Multiple Control Modes;
Dynamic: ◆ Torque Control
Static: ◆ Torque Control ◆ Torque Control + Angle Monitor
Torque Control Methods:
◆Closed-loop control with wireless transducer installed on the tool for
bolting joints with various joint hardness
◆Open-loop control without transducer installed on the tool but with the torque measured from a reliable source and operates under Air Pressure Mode for the unified type of joints in mass bolting tasks
Functions with remote configuration or monitoring with PC, smartphone, or tablet through Mobile APP are optional upon request
Operation records traceable through USB, Ethernet or exported to the cloud server through wired or wireless connections
except that there are no digital airflow meter and solenoid valve sets for various flow rate combinations.
Wireless Rotary Torque Transducer –
TTES/TTEH/TTEB/TTAS/TTAH/TTAB /TTER
Unique wireless feature sets a new standard for accurate static torque measurement and dynamic torque control for all continuous and discontinuous air-driven tools especially the impact or pulse tool, regardless of tool brand and its designed mechanism with proven satisfactory control accuracy and durability.
It fits in-line between the air-driven torque tool and the sockets or fasteners. Used with the TCA Torque Controller and closed-loop control for excellent torque control accuracy allowing the use of one torque tool among several joints with various hardness.
It solves the problem of the torque loss that may be caused by the variation in the joint hardness while bolting or the rise in temperature of hydraulic fluid in pulse tools or the posture of holding the tool during continuous operation and compensates the dynamic torque automatically within its allowable working torque range.
TTAS can be used along with a Dongle and Cellphone or Tablet and driven by a manual torque wrench to work as a digital torque wrench for static torque control and torque verification.
The patented control algorithm enables the operator to measure the tightened torque with TTAS at 0.5o angular movement to verify the most real and accurate torque applied to the bolt. This advanced feature provides an advantage overall digital torque wrenches on the market.
Key Features
Static torque control accuracy: ± 1% CW / ± 2% CCW
Static angle measurement range: 0∘~ 360∘
Patent-pending shock reduction design to withstand the violent vibration of impact tools. Applicable to any air-driven impact or oil pulse tools regardless of brand and the type of impact mechanism for torque calibration, measurement, control, and verification.
Applicable to any power torque tool with a built-in torque control mechanism for monitoring the bolting status and up-logging the data to PC/Tablet for data collection and further production management and job traceability.
The type and size of both ends can be custom-made.
The operation cycles and the over-torque information will be recorded for the ease of warranty judgment.
No-slip ring design, more durable under shock and vibration for long service life.
RF2.4GHz for transmitting torque and angle signal wirelessly within 15M working distance.
Power: 3.7V, rechargeable battery
TTAS/TTAH/TTAB is recommended for static torque control, measurement, and verification only.
TTES/TTEH/TTEB is applicable to any dynamic torque control with power torque tools.
TTER is specifically designed with an embedded Reader for reading and writing the data from the Sensing Bolt and Tagged Bolt throughout the bolting process.
Torque and Tension Tester- TTT
TTT is a unique device for measuring the dynamic torque capacity of any torque tools, manual, electric, cordless, and pneumatic. It will tell how soon the power-driven torque tool can reach its maximum torque.
It is equipped with the bolt and threaded bushing with correspondent size for each pair to simulate the bolting condition for more accurate torque and clamping force measurement.
The diagram will enable the user to realize the clamping force-induced under different torque for different sizes of threaded fasteners.
Torque Sensing & Transmitting Socket with Reader– TTER/TSSR
The patented socket designed for sensing and transmitting the torque signal to the Torque Controller – TCA for real-time closed-loop torque control. While applying to the innovative Tagged Bolt-TB or Sensing Bolt-SB, not only the bolting sequence can be programmed in the Torque Controller for selected stages of bolting by sequence, but also the bolting data along with the operator ID and the workpiece barcode can be recorded in the memory of the tag of TB or flash memory in the SB. All information can be uploaded to the peripherals or cloud server for tracking the relevant responsibility of work to ensure the highest quality and reliability of the joint.
Dongle – ZD
With the use of the Dongle attached to a PC/Tablet/Handset, any power torque tool with a built-in torque control mechanism, not only the bolting status throughout the process can be monitored and all data such as the workpiece and operator ID as well as the time and torque applied to the bolt can be recorded and uploaded to PC/Tablet/Handset simultaneously for further production management and job traceability.
Gateway – ZG
For the purpose of transmitting the bolting data from the Transducer and Sensing Bolt to peripheral devices and cloud server. Collect up to 10 devices at the same time.
Products Combination for Various Applications
Controller | Torque Tools | Torque Transducer | Interface | Data Collection | Applications |
TCA | Any Air torque Tool | TTAS/TTES | TF/TS | TCA | Torque Calibration prior to torque |
TCA | Any Air torque Tool | TTES | Socket / Bits | TCA | Torque Control during bolting process |
TCA/TTT | Manual Torque Wrench | TTAS | Socket / Bits | TCA/TTT | Torque Verification after bolted |
TCA/TTT | Manual Torque Wrench | TTAS | TM | TCA/TTT | High Torque Control / Verification |
TCA | Any Air torque Tool | TTES/TTEH/TTEB | Socket / Bits | TCA | Job Combination for work station |
TCA | Any Air torque Tool | TTER | TB | TCA | Bolt production and bolting data record Bolting Sequence Control |
TCA | Any Air torque Tool | TTER | SB | TCA | Bolt production and bolting data record Bolting Sequence Control Bolted joint status Remote Monitoring |
TCA | Any Air torque Tool | TTER | SB+TB mixed | TCA | Bolt production and bolting data record Bolting Sequence Control Bolted joint status Remote Monitoring |
Torque Control Mechanism Cordless Wrench | Torque Tool with built-in torque Control Mechanism | TTAS/TTES/TTEB | Socket / Bits / TM | Dongle + TTT Cell Phone / PC / TABLET | Monitoring bolting status, judge OK/NOK Workpiece and Operator ID Scan Bolted Torque and time recorded for production management ,time study and job traceability |
Power Torque Tools with Torque Limit Mechanism | Power Torque Tool with Torque Control Mechanism + Click Type Torque Wrench | TTAS | Socket / Bits / TM | Dongle + TTT Cell Phone / PC / TABLET | Verifying the Tightened Torque, Judge OK /NOK Workpiece and Operator ID Scan Bolted Torque and time recorded for production management ,time study and job traceability |
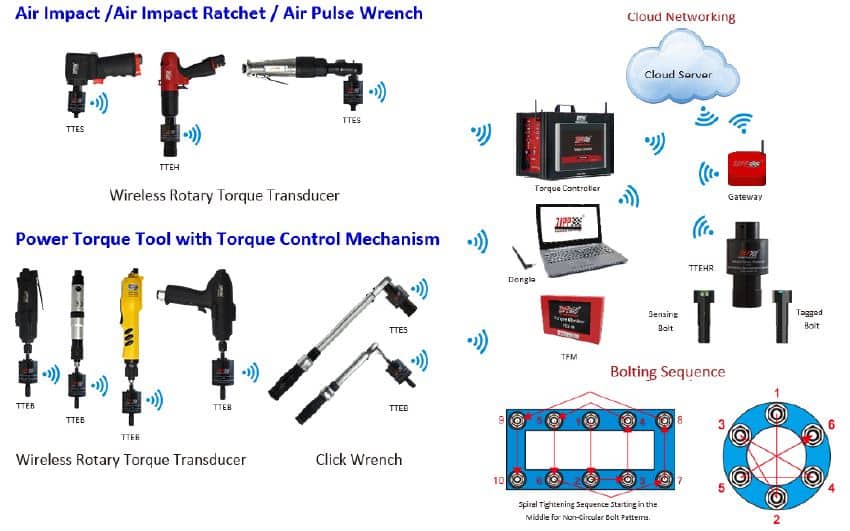
Common problems & solutions of bolting works
Problems | Solutions |
Hard to control the target torque accuracy due to the hydraulic fluid temperature rise in pulse tool which causes the torque to decline and torque created by uncontrollable air impact wrench mechanism which causes a considerably strong vibration during intermittent operation | Take advantage of ZIPPTORK Torque Controller-TCA & Wireless Rotary Torque Transducer-TTES, the sensed torque and angle signal will be transmitted from the TTE to TCA simultaneously and wirelessly while controlled by the patented control device and algorithm to effectively control any air-driven impact or oil pulse tool with satisfactory control accuracy within ±5% ~ ±15% |
Bolt joints characteristics – hard or soft joint, cause unstable torque controllability | The patented control algorithm and device on Torque Controller-TCA will compensate for the dynamic torque loss automatically to allow it to achieve the target torque range |
The torque control accuracy is always affected by the tool impact mechanism and the posture of how the operator holds the tool during operation | The closed-loop control and patented control algorithm enables the Torque Controller-TCA to control the torque accuracy effectively regardless of the tool brand and impact mechanism as well as the holding posture of the operator |
The operator didn’t follow the bolting sequence to fasten the bolts and led to uneven clamping force on the joints | Use the Torque Controller-TCA and the Torque Sensing and Transmitting Socket- TTER/TSSR along with the Tagged Bolt-TB or Sensing Bolt-SB, the bolting sequence and stage of bolting can be programmed in advance, not only the operator has to obey the bolting sequence, but also the torque can be appropriately controlled at each stage. The bolting data can also be recorded for traceability to verify the responsibility of fastened joints to ensure the highest quality and reliability of bolting |
The torque controller needs to be paired with specific torque tool | TCA applies to any air driven torque tool regardless of the brand and its mechanism |
Bolting Issues with Power Torque Tools
Q & A
How to control the output torque of an impact wrench?
ZIPP’s Torque Controller∼TCA + Wireless Rotary Torque Transducer∼ TTES with the patented control apparatus and the algorithm will enable you to control oil Pulse tools torque within ±5~ 10% accuracy and ±10~ 15% for air impact wrenches.
How to do the bolting sequence control & tighten the bolt in several runs?
With the programmable Torque Controller∼TCA + Wireless Rotary Torque-Sensing and Transmitting Socket∼ TTER +Tagged Bolt∼TB, not only the bolting sequence but also the torque to be applied within several runs can all be programmed in advance.
How to control the joint tightness effectively?
With the Torque Controller∼TCA + Wireless Rotary Torque-Sensing and Transmitting Socket∼TTER + Sensing Bolt∼SB, it will assure that a homogeneous clamping force can be fulfilled.
How to control the bolting torque on the tire stud and monitor the status of the bolted joint as the function of the tire pressure monitoring system (TPMS)?
With the Torque Controller∼TCA + Wireless Rotary Torque-Sensing and Transmitting Socket ∼TTER + Sensing Bolt∼SB + Transmitting Cap∼TC, it will not only ensure that the clamping force can be applied evenly on each bolt/stud but also the joint status can be monitored remotely by the car computer.
How to monitor the bolted joint status periodically & remotely?
With the Torque Controller∼TCA + Wireless Rotary Torque Sensing and Transmitting Socket∼TTER + Sensing Bolt∼SB + Transmitting Cap∼TC + Gateway∼ZG, the joint status can be monitored remotely and periodically.
How to trace the responsibility of the bolting work after bolted?
Use the Wireless Rotary Torque Sensing and Transmitting Socket∼TTER with the features of the Tagged Bolt∼TB & Sensing Bolt∼SB, not only the production record of the bolt, but also the bolting process and its result can be recorded in the memory of each bolt for traceability to verify the responsibility and cease the controversy if there is any.
How to monitor the bolting status of a power clutch type torque tool?
With the Wireless Rotary Torque Transducer∼TTES/TTEB + Dongle∼ZD to PC/Tablet/Handset, the bolting status of a power clutch-type torque tool either electric or pneumatic can be recorded simultaneously during work. The data can be collected for production control and time study to improve productivity.
How to collect bolted data with the torque tool which has a built-in torque limit mechanism?
Use the Wireless Rotary Torque Transducer – TTES/TTEB with a manual, electric, or pneumatic torque tool while bolting, the bolted data can be recorded immediately after bolted and transmitted to the PC/Tablet/Handset via a Dongle, then, uploading to other peripheral devices.
How to collect the bolted torque data tightened with a click wrench?
Use the Wireless Rotary Torque Transducer∼ TTAS with a click wrench, the audible “ CLICK” sound can be detected and become the visible bolted data and transmitted to the PC/Tablet/Handset via a Dongle while verifying if it’s OK or not. The collected data can be uploaded to peripheral devices for traceability.
How to verify the residual torque of a bolted joint?
Use the Wireless Rotary Torque Transducer∼ TTAS with a manual torque wrench, the data will be transmitted to the PC/Tablet/Handset via a Dongle to verify if it’s OK or not. The collected data can be uploaded to peripheral devices for traceability.
Applying the most advanced bolting technology
